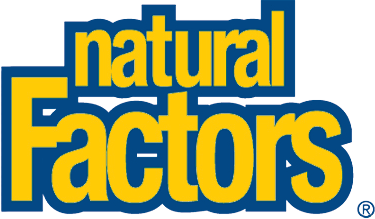
Success Story
Heat Recovery Reduces Steam Consumption in Tunnel Wash System
Today, Natural Factors is one of the largest manufacturers of nutritional products in North America.
Their origins reach back to the 1950s, and right from day one, they’ve always been fully committed to making products right. Natural Factors is not a public company with shareholders to impress. Instead, they care about impressing you. They have close to 700,000 square feet of space across nine locations in North America housing offices, manufacturing and production facilities, laboratories, distribution centres, and extensive warehouses. The head office is in Coquitlam, British Columbia.
Marc Giron, Chief Engineer at the Coquitlam plant was interested in reducing his plant steam consumption. His company’s success was taxing his boiler capacity fast and a project was being developed to add an additional boiler. In the meantime he was looking for cost effective projects with quick paybacks to assist him in his goal – reduce steam consumption but maintain factory output. Mark called Andrew Reynolds to have a conversation to discuss his options. After walking the plant and in learning about the production processes and the various areas of steam consumption a proposal was made. Reclaim the waste heat from the tunnel and cart washers. A detailed cost analysis was made looking at the number of Btu’s that would be recaptured including the installation and equipment costs. The result was a unique energy saving heat exchanger system that was installed and reduced overall steam consumption by 50% for the washing systems. The cold water makeup was now 100% preheated during normal operation. This success was achieved by recapturing valuable heat content from the overflow rinse water.
This type of heat recovery system is now standard with many tunnel and cart washer manufacturers. Marc’s project earned a 6 month payback. Natural Factors installation of an additional boiler went ahead the next year. The heat recovery system continues to this day to save the company money with reduced steam demand for cart and tunnel washing.
Did You Know?
Consider Installing High-Pressure Boilers with Backpressure Turbine-Generators
When specifying a new boiler, consider a high-pressure boiler with a backpressure steam turbine-generator placed between the boiler and the steam distribution network. The turbine does not consume steam. Instead, it simply reduces the pressure. In essence, the turbogenerator serves the same steam function as a pressure-reducing valve (PRV)—it reduces steam pressure—but uses the pressure drop to produce highly valued electricity in addition to the low-pressure steam. The economics depends on the steam consumption rate in the plant.