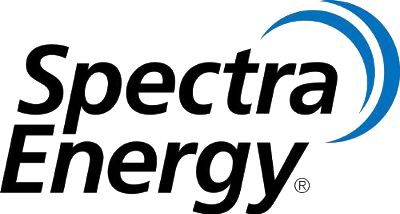
Success Story
Pressure Powered Pump Extends life of Heat Exchanger in Amine Reboiler at McMahon Gas Processing Plant
Spectra Energy’s BC Pipeline and BC Field Services businesses are an integral part of B.C.’s natural gas midstream industry, strategically located to connect vast supply with growing demand.
The McMahon plant is the first natural gas facility constructed in BC. It has a processing capacity of 810 MMcf/d with recovery of up to 98% sulfur.
The west amine reboiler for gas train 1 has been selected historically to study the effects of equipment changes in the effort to improve process efficiencies and extend equipment life that is involved in the removal process of sulphur from the raw gas field network. The amine reboiler process is critical to sweeten the gas before transport in the main distribution pipeline. Andrew Reynolds relationship with the plant and his experience and knowledge of steam applications and condensate removal was key to the plant contacting him for advice. The heat exchanger tube bundles were lasting less than a year and the plant manager was looking for solutions to extend the bundles life. Upon investigation, it was apparent the heat exchanger system was running completely flooded. This will not only lead to corrosion and reduced tube bundle life but also decreased production in the reboiler still. The solution was immediately apparent to Andrew. A proposal was made to install a quad condensate removal pump package system. This system will provide effective condensate drainage under all load conditions including vacuum.
It was during start-up and commissioning of the new condensate removal system that the tube bundle level gauge used to monitor the degree of flooding dropped to zero. It was noticed by one of the Spectra Gas train operators who yelled out “What happened to the condensate – is the steam valve open!??” It was, and the condensate did not remain in the tubes anymore. This solution solved the issue of reduced output, extensive bundle corrosion, costly repairs and downtime.
Did You Know?
Use a Vent Condenser to Recover Flash Steam Energy
When the pressure of saturated condensate is reduced, a portion of the liquid “flashes” to low-pressure steam. Depending on the pressures involved, the flash steam contains approximately 10% to 40% of the energy content of the original condensate. In most cases, including condensate receivers and deaerators, the flashing steam is vented and its energy content lost. However, a heat exchanger can be placed in the vent to recover this energy.